WHAT WE CAN DO WITHIN OUR COVERED AREA
A quick overview to our fabrication process:
Our Staff
– 125 personnel (30 engineers, 5 technicians, 75 workers, 15 others)
– Engineers (30) and Technicians (5)
- 12 Design Engineers
- 5 Project Engineers
- 5 Fabrication Engineers
- 5 Quality Control Engineers
- 2 Purchasing Engineers
- 1 Welding Engineer
– Administration staff and others (15)
– Workers (75)
- 30 Stainless Steel fabrication (10 welders)
- 30 Carbon Steel fabrication (10 welders)
- 4 Painters
- 4 Machining
- 7 Others (Cutting, packing, cleaning, etc)
– Monthly labor capacity 18.000 manhours
-Annual labor capacity 216.000 manhours (without extra time)

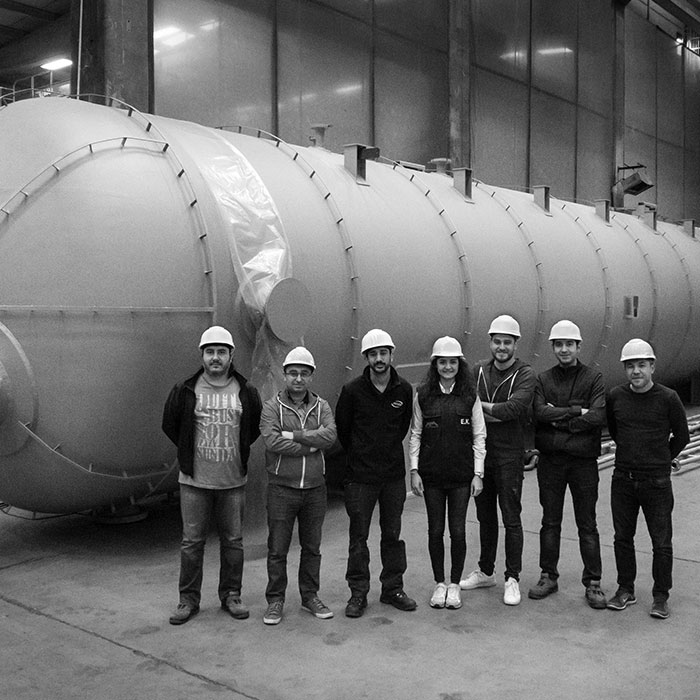
Our Process
- Mechanical and Thermal (if required) design studies, FEA analysis per related codes
- Drawings preparation
- Fabrication planning
- Welding document preparation
- Quality control documents preparation
- Customer approvals
- Material purchasing
- Material receiving inspections per codes
- Fabrication drawings preparation
- Fabrication (Cutting, bending, machining, welding, assembly, etc.)
- Third party inspections per approved Inspection Test Plan (ITP, Traveler)
- Preparation of customer biweekly reports
- Testing
- Any internal linings (rubber, ebonite, refractor, etc.)
- Cleaning, passivation, sand blasting & painting or polishing
- Quality dossier preparation
- Packing
- Delivery
Materials of Construction
- Carbon Steel for Low and High Temperatures
- Special HIC (Hydrogen Induced Cracking) resistant carbon steels for lethal services
(for WetH2S, Amine, Hydrogen, Toxic, Caustic services)
- Austenitic Stainless Steel
- Martensitic Stainless Steel
- Ferritic Stainless Steel
- Duplex and Super Duplex
- Monel
- Nickel and Copper-nickel Alloys
- Low and High Alloys Steel
- Hastelloy and Incoloy
- Carbon Steel Base Cladded Steels (Roll bonded or Explosion bonded)
- Titanium
- Hardox
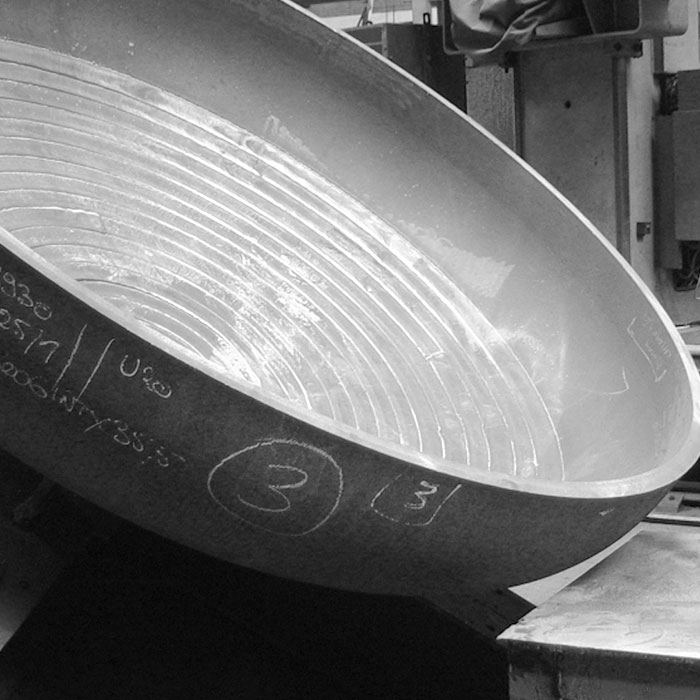
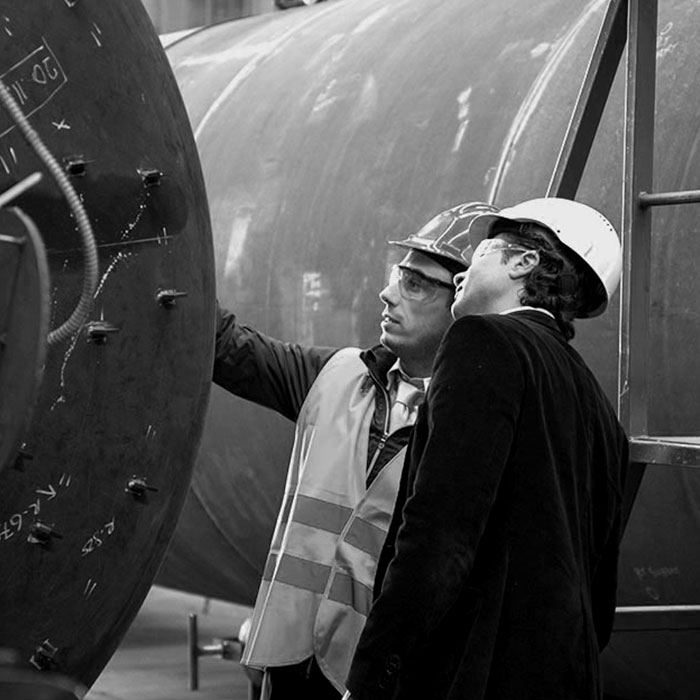
In House Ispection Activities Performed
- Visual Inspection
- Ultrasonic Test
- TOFD / PA
- Dye Penetrant Test
- Magnetic Particle Test
- Positive Material Identification (PMI Test)
- Ferrite Check
- Clad thickness measurement
- Radiographic Test (X-Ray)
- Hardness Tests
- Mechanical Tests
- Surface Roughness Tests
- Charpy Impact Tests
- Chemical Tests
- Corrosion Tests (HIC / SSC)
- Bubble Test
- Pneumatic Test
- Hydraulic Test
- Vacuum Test
- Instruments Calibration
- Third Party Inspections
In-house fabrication capabilities
- Welding (TIG, MIG, MAG, SAW, TIP-TIG, Orbital TIG) (Qty:66 // 24 GMAW, 29 GTAW, 2 SAW, 10 SMAW, 1 Aluminum)
- Strip Cladding SAW (45mm)
- Weld preparation tools (Qty: 2)
- Oxyfuel cutting (Qty: 2)
- Plasma cutting (Qty: 1)
- Laser cutting (subcontracted)
- Waterjet cutting (subcontracted)
- Shears (separate for carbon and stainless steels) (Qty: 2)
- Plates Rolling (separate for carbon and stainless steels) (Qty: 3)
- Beveling (Qty: 2)
- Bending (Qty: 3)
- Tubes expanders (Qty: 2)
- Heat Treatment (Local and Furnace)
- Horizontal Lathes (Qty: 2)
- CNC Plasma Cutting Machines (Qty: 1)
- CNC Milling Machines (Qty: 2)
- CNC Lathe (Qty: 2) Drills with BOM (Qty: 2)
- Milling machine
- Positioners (Qty: 2)
- Rotators (Qty: 10)
- Presses (Qty: 2)
- Sand Blasting Unit (Qty: 1)
- Airless painting tools (Qty: 3)
- Passivation tools
- Polishing tools
- Magnetic Drills (Qty: 6)
- Overhead Cranes (10 tons, 20 tons, 35 tons, 40 tons)
- Burners, Compressors, Generators, Dyers
- Various others
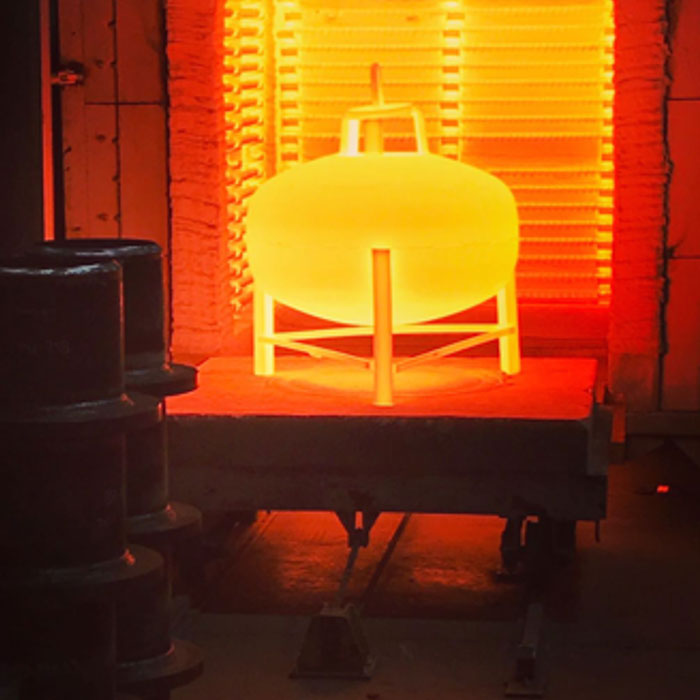